Meet the COLUMBIA INDUSTRIAL Colour Match Team
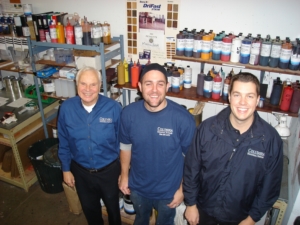
MIKE TREVOR JOSH
We Match Stains: To Columbia Wiping Stains, Becker Acroma’s Arti® Spray & Wipe
Alcohol Stains, Aqua Chroma® Water Based Stains, Microtoners,
Glazes & Tinctures.
We Match Paint: To Becker Acroma’s pigmented enamels: Matador® and Strong® .
Matching colours is tricky!
Think of it for a moment; there is, in theory, an almost infinite number of colours, shades, tones etc. While basic colour theory can be helpful, it can only take you so far. Industrial pigments and dyes don’t come in “basic” colours, but instead we work with such exotically named pigments as “burnt umber” and “red oxide” all of which are variations of prime colours.
How do we do it?
This is where patience and experience are key. While the process may appear to be simple, just adding a little of this and a little of that, in reality, colour matching can be challenging. Unlike retail paint stores who use a volume-based approach (those familiar cylindrical pigment dispensing machines), we weigh all our pigments and dyes to an accuracy of 1/100th of a gram. This ensures that we can accurately replicate any of our colour matches. When developing an initial colour match, we record the weights in our computer files. The resulting “formula” then becomes part of our colour data base that includes literally thousands of colours.
What do I need to supply?
For stain matches, it is essential that we work with an actual sample of the wood that is to be stained as the chemical composition of wood can have a marked effect on the resulting colour of a given stain. Please give us a sample of the “target colour” and some pieces of the wood that you will be staining.
For paint matches, a sample of the actual paint or the paint manufacturer’s colour reference number and name. For example: Benjamin Moore HC- 27 “Monterey White” or Cloverdale 7300 “Jet Stream” or M.L. Campbell 1115 “Quartz Moon”. Occasionally, paint companies change their fan decks and/or their referencing numbers. It is important to keep fan decks current-or if in doubt, check with us first. Lighting can have a major impact on the viewer’s perception of colour. The more pigments and dyes in paint, the more impact varying light will have on the apparent colour so let us know what the application will be.
How long will my match take?
There are several factors that determine our “turn-around time” for a colour preparation. If it just involves mixing to an existing formula (either a stain or a paint), then orders received before 11:00 AM can be completed on the same day. On the other hand, if we need to match to a sample of stain or paint, every case is different. Some matches can be done quite quickly, while others can require many iterations before we are satisfied with the result. And then there is the work load factor, which we can’t predict from day to day. While we can usually get a match done within a couple of days – (sometimes sooner; sometimes a bit longer), the bottom line is that we pledge to do our very best – all the time.
How much will it cost?
No charge for Becker Acroma lacquer customers. If you are outside the Victoria area you’ll need to cover the courier costs unless one of us is in your area and can pick-up your sample. If you are not a lacquer customer a nominal colour match charge plus material costs may be applied for a one litre minimum size sample.
Open 7:30 – 4:30 Monday – Friday, 8:00 – Noon Saturdays